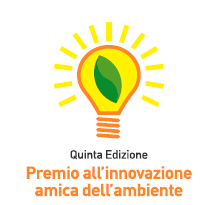
|
Scheda
progetto
Marconi Di Garzitto Giancarlo &c. S.a.s. Dai rifiuti/le risorse
Informazioni sul candidato: |
Ragione sociale |
Marconi Di Garzitto Giancarlo &c. S.a.s.
|
Settore |
Riciclaggio materie plastiche provenienti da post consumo
|
Sito web |
http://www.marconitalia.com |
Attivita dell'impresa |
La società so occupa da 15 anni di riciclo e riutilizzo di materiale plastico proveniente da post-consumo, con il materiale plastico recuperato realizza sedili e schienali per ogni tipo di sedia che vengono esportati in tutto il mondo. Si recuperano 20.000 tonnellate all'anno di plastiche eterogenee, che diversamente verrebbero smaltite in discarica o inviate a termo distruzione (viene recuperato lo scarto di selezione dei centri di raccolta). La società utilizza impianti e macchinari ad alto contenuto tecnologico, progettati e costruiti su disegni e disposizioni del proprietario della società (Garzitto Giancarlo) che detiene i brevetti
|
Certificazioni |
|
Forme di controllo della gestione |
controllo della gestione dei processi di recupero da parte di società specializzata inviata da COREPLA con cadenze mensili
|
Certificazioni del prodotto |
|
Informazioni sull'innovazione: |
Titolo |
Dai rifiuti/le risorse
|
Presentazione dell'innovazione |
"Riciclaggio del Pulper", l'innovazione consiste nell'aver ideato un processo produttivo esclusivo che va a riciclare uno scarto dello scarto, infatti il pulper è lo scarto che si ottiene dal riciclo della carta: l'innovazione permette di portare a nuova vita la fibra di carta scartata e a recuperare tutta la plastica presente nel pulper.
|
Progettista |
|
Innovazione di |
prodotto
|
Tema |
Design per la sostenibilità ambientale
|
Descrizione dell'innovazione |
Il processo produttivo si compone delle seguenti fasi: 1. arrivo e stoccaggio delle materie prime in un'apposita vasca posta all'interno del capannone e costruita in cemento al fine di evitare percolazioni; 2. inzuppamento: il materiale viene traposrtato in una vasca di acciaio inox piene d'acqua dove rimane in ammollo per circa 3 ore; 3. mulino lento: il materiale viene traposrtato a un nastro elevatore che alimenta un mulino lento dove viene sminuzzato e frantumato in modo da ottenere materiale di pezzatura idoneo alle successive lavorazione; 4. deferizzazione e desabbiatura: tramite nastro traposrtatore il materiale viene inviatoai deferizzatori e a un sabbiatore con lo scopo di eliminare i metalli ferrosi, i metalli non ferrosi e gli inerti. Il materiale è poi inviato per mezzo di un sollevatore a nastro in una vasca che fa da bacino d'alimentazione, polmone, ad un trasportatore redler il cui compito è servire ciascuna delle linee di separazione previste; 5. centrifuga: il materiale è poi inviato al fulcro dell'impianto una serie di quattro centrifughe che hanno lo scopo di separare la plastica e i prodotti non fibrosi dalle fibre cellulosiche che successivamente subiranno differenti trattamenti; 6. vasca di decantazione: la parte composta da plastica e da materiali non fibrosi viene immessa in una vasca di decantazione dove, in base al peso specifico, avviene la separazione fra "plastiche nobili", più pesanti e leggere, quest'ultima tenderà a galleggiare sull'acqua mentre la parte più pesante scenderà sul fondo; 7. seconda centrifuga: la parte leggera viene nuovamente centrifugata per dividere ulteriore parte cellulosica dalla plastica e eliminare una considerevole parte d'acqua presente in esso; 8. essiccazione, presa, granulazione: una volta centrifugato il materiale viene essiccato e successivamente trasferito alla pressa dove due rulli spingono il materiale attraverso una matrice anulare che lo sintetizza ed essicca per frazionamento. Il materiale potrebbe essere successivamente inviato in un silos in attesa di essere avviato alla granulazione po poter così ottenere plastica in granuli; 9. macinazione, essiccazione, insaccaggio: la parte pesante viene macinata, essiccata, la plastica micronizzata così ottenuta viene insaccata; 10. grigliatura, microfiltrazione, filtro pressa: le fibre cellulosiche e l'acqua
in uscita dalle centrifughe vengono inviate all'impianto di depurazione; 11. impianto di depurazione: la prima fase di trattamento delle acque è la di sabbiatura dove è eliminata l'ulteriore parte di materiale inerte residua. la miscela di fibre cellulosiche-acqua viene poi fatta passare attraverso una griglia di separazione dive vengono recuperate le fibre cellulosiche più lunghe di maggir qualità che vengono compattate e stoccate in un apposito contenitore. Successivamente l'acqua contenenete ancora una parte fibrosa viene microfiltrata, poi fatta decantare e chiarire in un sedimentatore lamellare a flusso ascendente. Qui le restanti fibre cellulosiche si depositano sul fondo venendo poi inviate alle vasche di ispessimento e al filtro pressa, dove con l'aggiunta di farina di legno vengono disidradate e rese sottoforma di pannelli. L'acqua reflua depurata verrà poi nuovamente immessa nel ciclo produttivo, con un consumo di 1 metro cubo al giorno per evaporazione.
|
Data della prima realizzazione |
settembre 2004
|
Benefici ambientali |
Benefici ambientali |
Sì |
No |
Minor consumo energie non rinnovabili |
|
|
Diminuzione scarichi inquinanti |
|
|
Riduzione rifiuti prodotti |
|
|
Ricorso energie rinnovabili |
|
|
Minor consumo materie prime |
|
|
Ricorso a risorse locali |
|
|
Miglior uso infrastrutture esistenti |
|
|
Minor ricorso a trasporto e logistica |
|
|
|
Valutazione dell'impatto dell'innovazione sul sistema |
|
Altri attori sociali coinvolti per la promozione e lo sviluppo dell'innovazione |
Vengono coinvolti:
Assocarta (Associazione Italiana fra gli Industriali della carta, cartoni e paste per carta aderente a Confindustria)
Polieco (Consorzio per il Riciclaggio dei Rifuitio di Beni in Polietilene)
Università degli Studi di Udine (Ingegneria Gestionale)
|
Politiche di comunicazione ambientale e sociale adottate |
In gran parte sono state effettuate comunicazioni di progetti2005 mediante partecipaziopne a concorsi e presentazione dei progetti2005 ad enti pubblici, quali le università, le provincie ed i comuni.
|
< Indietro
|